Wall Sections: What they are and How to Draw Them
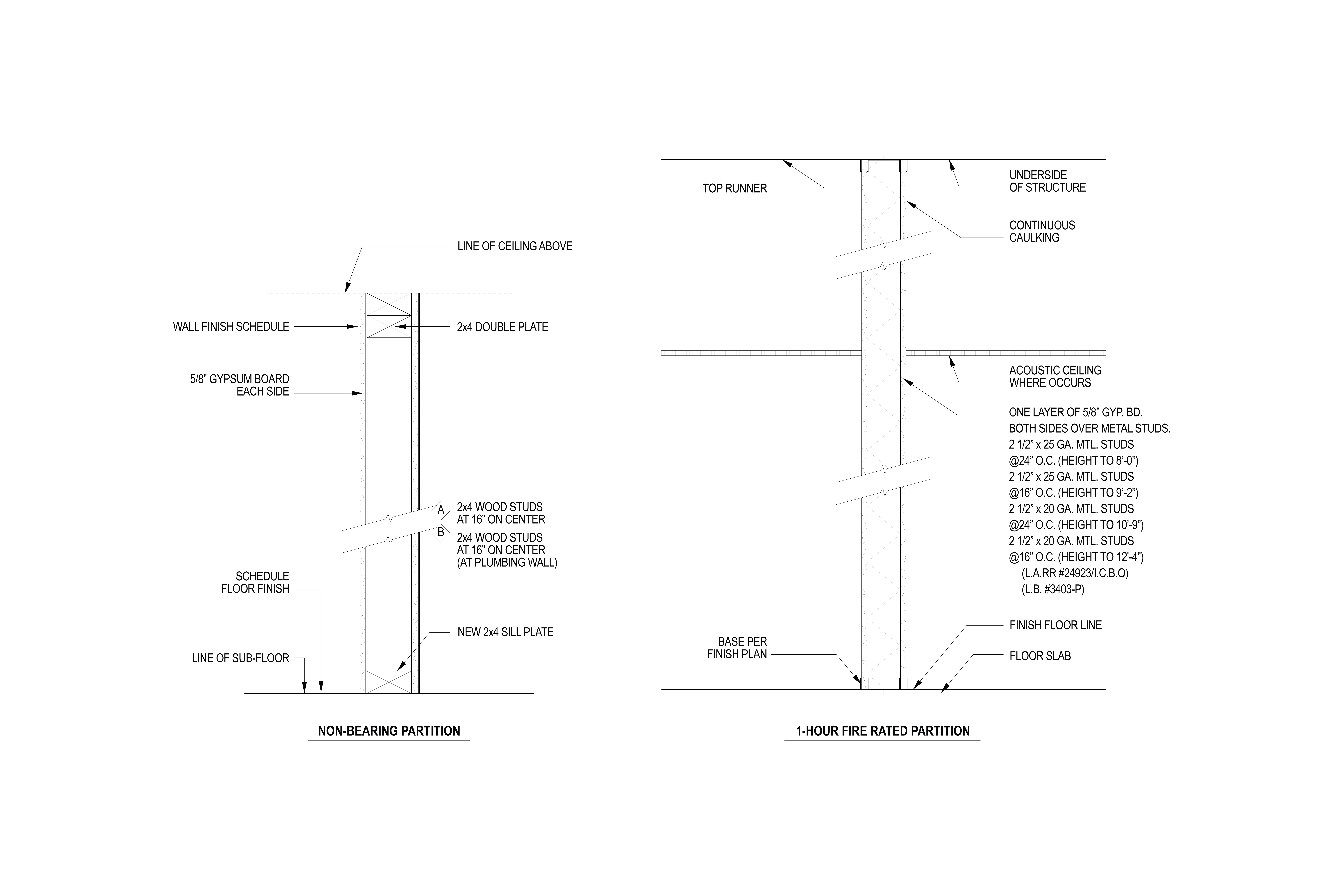
Overview
Have you ever wondered about the process involved in creating the walls that surrounds us? What materials are they made up of? Then you are in the right place. Wall sections are the blueprint of a building's structure, from the materials that comprise each layer to the methods employed to guarantee structural integrity and insulation.
Every component of a wall section, from the inner layers of insulation to the external facade, has a distinct function and adds to the overall strength and performance of a building. We can better understand how architects handle issues like sound insulation and weatherproofing while embracing sustainable methods by looking at various types of materials.
This article will delve into the intriguing details of wall sections, revealing their function in building and design, as well as their components and offering some extra advice on how to draft those mighty wall sections.
Take a journey with us as we uncover the mysteries surrounding one of the most essential components of our built environment, whether you're an experienced architect seeking to broaden your knowledge or you're just inquisitive about how buildings are constructed.
What is a wall section?
A wall section typically refers to a detailed drawing of vertical slice or cross-section of a building’s wall. A wall section illustrates each component such as material, finish, structure, insulation, and other relevant details that make the structure of a wall. A wall section provides a comprehensive understanding of how walls are connected and function within a building. Additionally, it might include details about window and door openings, flashing, and waterproofing measures to ensure proper weatherproofing and moisture management.
Purpose of a wall section in architecture or construction documents
Wall sections play a crucial role in architecture and construction documents. Their primary purposes include:
Construction Details: The integration of different parts, materials, and systems to create a wall assembly is demonstrated by a wall section. It gives builders comprehensive details regarding the placement of structural components, insulation, finishes, utilities, and openings, assisting them in building the wall precisely.
Integration of Building Systems: The wall section demonstrates how the various building systems of the wall assembly, including the structural, mechanical, electrical, plumbing, and fire safety systems, are interconnected. This makes it easier for different trades to coordinate and guarantees that all the parts function as a whole.
Structural Integrity: Wall sections show how structural components like studs, beams, and foundations are arranged. These components are essential for maintaining the weight of the building and withstanding outside forces like seismic and wind stresses. Wall sections guarantee that the wall can bear expected loads and retain structural integrity over the course of its life by outlining the structural components.
Building Performance: Each element within a wall section contributes to the overall performance of the building. Insulation materials regulate thermal energy transfer, vapor barriers prevent moisture infiltration, and air barriers control airflow, thereby enhancing energy efficiency and indoor comfort. Understanding these elements allows designers to optimize building performance and meet energy efficiency goals.
Material Selection and Integration: Wall section facilitate the selection and integration of appropriate materials for different building components. Whether it's choosing exterior cladding, insulation types, or interior finishes, understanding how materials interact within the wall assembly ensures compatibility, durability, and aesthetic coherence throughout
Coordination: The wall section communicates crucial information to various stakeholders involved in the project. It serves as a reference point to align their individual designs and verify their consistency and adherence to project specifications. For example, Structural engineers may review the wall section to confirm that the framing members meet load-bearing requirements, while mechanical engineers may coordinate the placement of HVAC ducts and vents within the wall cavity. This coordination helps prevent conflicts and ensures that all systems work harmoniously within the building envelope.
Code compliance: Wall sections help ensure compliance with building codes, regulations, and industry standards. They incorporate details related to fire resistance, thermal performance, sound insulation, structural integrity, and other requirements mandated by local building authorities.
Quality Assurance: Quality assurance is a critical aspect during construction. Wall sections facilitate quality assurance by providing a comprehensive depiction of wall assemblies. They enable project teams to identify potential issues or discrepancies early in the process, allowing for timely adjustments and corrections.
Difference between wall section and building section
Both wall sections and building sections are important architectural drawings in a construction document, that serve important purposes. While a wall section focuses specifically on composition of a single wall or portion of wall in a building, on the other hand building sections depict the vertical slice through an entire building.
A wall section depicts the layers of a wall, materials etc., and a building section shows the number of floors, interior spaces, structural elements and overall layout of the building in a vertical perspective.
Wall sections are essential for understanding construction details, building performance, and compliance with building codes and standards. While building sections are useful for understanding spatial organization, vertical circulation and connectivity between different floors.
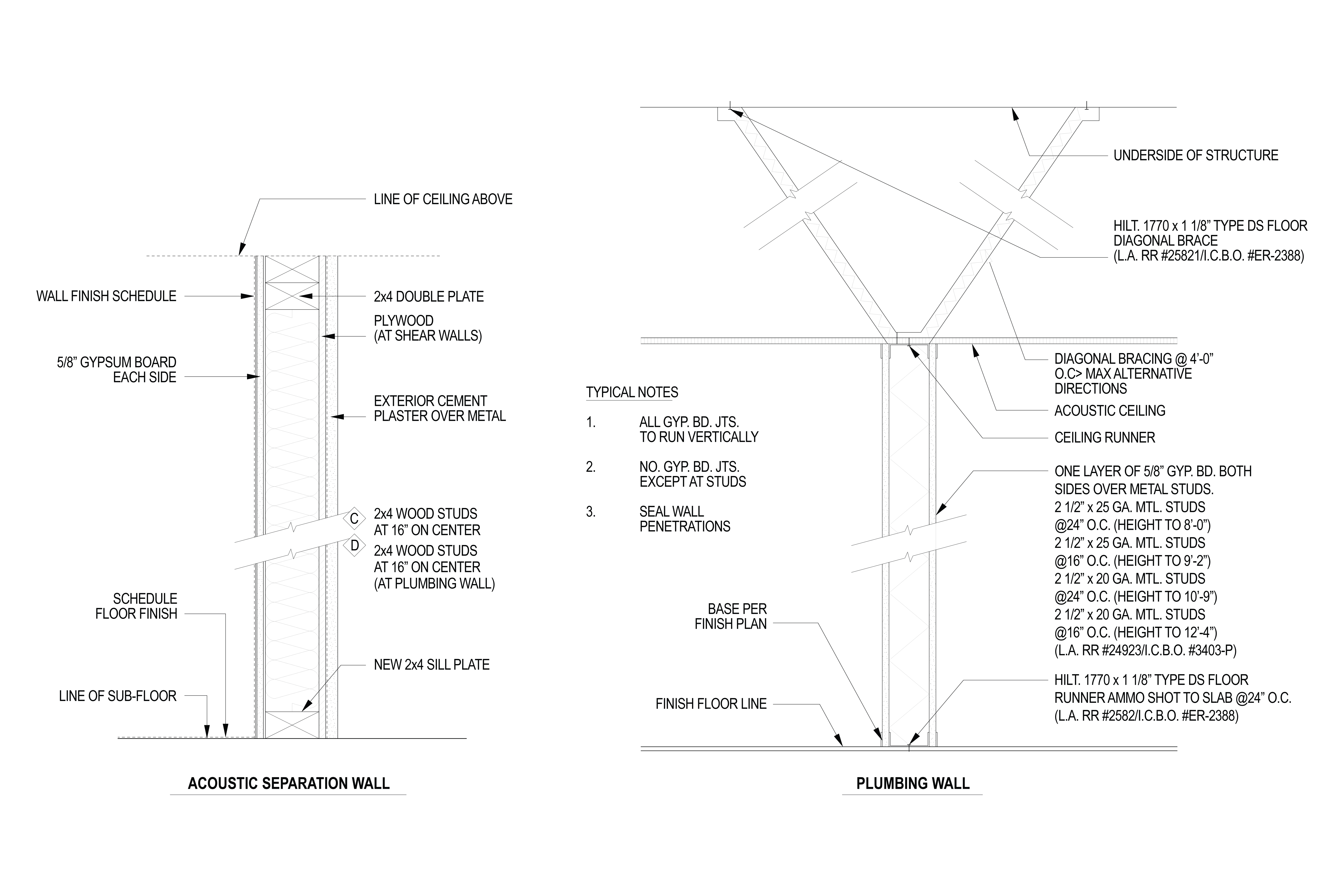
Typical Wall section
A typical wall section applies to the entire building unless it’s indicated elsewhere to refer to a different drawing. It usually cuts of the exterior/interior walls from the roof down through the foundation. The typical wall section also shows the number of stories and the type of foundation. This wall section detail doesn’t need to be keyed into the plans because it is the default construction for the building. Additional wall sections need to be drawn where conditions differ from the typical.
Components to consider in a wall section
Wall sections provide a detailed cross-sectional view that showcases various components. Each component plays a vital role in ensuring the wall’s stability, durability and functionality in the overall building structure. The components of a wall section can vary depending on factors such as building design, construction material and local building codes Let’s delve deeper into common components of a wall section:
Exterior Finish cladding: This is the outermost layer of a wall, it provides aesthetic appeal and protection to structure from environmental factors such as rain, sun, snow etc., common exterior finish material are brick, stucco, stone, siding-wood, vinyl and various metal panels.
Exterior Trim and Molding: Decorative elements installed on the exterior of the wall to enhance architectural aesthetics. Exterior trim and molding may include features such as cornices, window trim, or decorative moldings.
Interior Finish: The final layer applied to the inside of the wall, providing a decorative and functional surface. Materials may include drywall, plaster, paneling, or decorative finishes.
Insulation: It is placed within the wall cavity to improve energy efficiency by preventing heat transfer. Different Insulation materials offer varying level of thermal resistance and can be chosen based on factors such as climate, budget, and installation requirements.
Structural framing: The framework of the wall, which may consist of wooden or metal studs, columns, beams, or other load-bearing elements. The framing provides support for the wall and distributes loads to the foundation.
Vapor Barrier: A material that prevents moisture vapor from penetrating into the wall assembly, usually installed on the warm side of the wall to prevent condensation within the wall cavity.
Sheathing: Provides structural support and serves as a base for exterior finishes. Materials may include plywood, oriented strand board (OSB), or gypsum board (drywall).
Air Barrier: Controls airflow through the wall assembly, improving energy efficiency and preventing drafts. Materials may include house wrap, taped seams, or specialized membranes.
Moisture Barrier: Protects the wall assembly from moisture intrusion, typically made of materials resistant to water such as paints, coatings, or membranes.
Flashings: Materials used to direct water away from vulnerable areas of the wall, such as openings or junctions with other building elements. Common types include drip edge flashings, window and door flashings, and through-wall flashings.
Cavity Drainage Systems: Manage water that penetrates the wall assembly, particularly in below-grade or retaining walls. Systems may include drainage mats, weep holes, or pipes to channel water away from the structure.
Fire stop: Materials installed within wall assemblies to prevent the spread of fire and smoke between compartments or floors. Fire stops are typically located at penetrations such as pipes, ducts, or electrical conduits passing through the wall.
Soundproofing Materials: Insulating materials designed to reduce the transmission of sound through the wall assembly. These may include specialized acoustic insulation, resilient channels, or double-wall construction.
Expansion Joints: Gaps or joints in the wall assembly that accommodate thermal expansion and contraction, seismic movement, or settlement of the building. Expansion joints help prevent cracking or damage to the wall.
Termite Barrier: Protective measures installed to prevent termite infestation and damage to wooden components of the wall assembly. Termite barriers may be physical barriers or chemical treatments applied to the soil or building materials.
Electrical Conduits and Boxes: Channels or pipes embedded within the wall for routing electrical wiring. Electrical boxes provide junction points for connecting electrical outlets, switches, and fixtures.
Plumbing Pipes and Fittings: Pipes and fittings for conveying water, gas, or sewage within the wall assembly. Plumbing components may include water supply lines, drainpipes, vents, and fixtures such as sinks or toilets.
HVAC Ductwork: This refers to the ducts used in buildings to distribute hot or cold air. Depending on how the system is designed, HVAC ductwork may be placed next to the wall or inside the wall cavity.
Important details in wall section
Foundation: In a wall section, it usually depicts the type, depth, reinforcement, materials utilized and how it connects to the wall above it.
Waterproofing: It is a major component of the wall section, encompassing both internal and external surfaces. While interior waterproofing may include tanking systems, sealants, or waterproof membranes to guard against moisture penetration, exterior waterproofing uses membranes, coatings, and drainage systems to stop water infiltration.
Floor Systems: In a wall section, this illustrates the differences in floor heights and building techniques between levels by showing the floor construction for each level, including floor framing, subflooring, and flooring materials.
Mechanical, Electrical, and Plumbing (MEP) Systems: Including details of MEP systems passing through or within the wall assembly, such as ductwork, pipes, conduits, and electrical panels, shows their routing and integration with structural and architectural elements in a wall section.
Ceiling Construction: Illustrate the materials, insulation, and support systems such as ceiling joists or trusses and their connections to the roof and wall.
Window and Door details: In a wall section, the details of window and door depict the opening, framing, flashing, and trim details. These details also illustrate the connection of the window or doors with wall at lintel and sill level emphasizing the heights of window and door from floor level.
Roof Assembly: In a wall section, a roof assembly detail highlights the connection between the wall and roof components, such as flashing and fascia.
Tips to draw a wall section
Start with Clear Dimensions: Begin by determining the overall dimensions of the wall section, including height, width, and depth. Use a scale that allows you to accurately represent the components while fitting them on the drawing sheet.
Use Proper Scale: Choose an appropriate scale for the drawing to ensure clarity and readability while accommodating all the necessary details. Common scales for wall section include 1/4" = 1'-0" or 1/2" = 1'-0".
Identify Components: Identify all the components that need to be included in the wall section, such as structural elements, insulation, barriers, finishes, utilities, and openings.
Detail Components and Connections: Show how different materials and components connect and interact, like how cladding is fixed to sheathing or how insulation fits between studs.
Establish Layering Sequence: Determine the layering sequence of the wall assembly, starting from the exterior finish and progressing inward. This helps organize the components and ensures clarity in the drawing.
Include Structural Details: Illustrate the arrangement of structural elements such as studs, beams, columns, and foundations, along with connections and load-bearing capacities. Highlight any seismic or fire protection measures.
Show Material Transitions: Clearly depict transitions between different materials and layers, such as where exterior cladding meets sheathing or where flooring transitions to walls.
Provide Annotations and Labels: Label each component and layer clearly to indicate materials, dimensions, and other relevant information. Use annotations, callouts, and symbols to provide additional details where necessary.
Highlight Waterproofing and Drainage: Emphasize waterproofing membranes, coatings, and drainage systems applied to the wall assembly to prevent moisture infiltration and protect against water damage.
Simplify Complex Details: Break down complex details into simpler elements for easier understanding. Use exploded views or enlarged details where necessary to clarify intricate connections or assemblies.
Consider Cross-Sections: If the wall section intersects with other building elements such as roofs, floors, or windows, consider drawing cross-sections to illustrate the connections and transitions accurately.
Review Building Codes and Standards: Ensure compliance with local building codes and standards while drawing the wall section, particularly regarding fire safety, accessibility, and structural requirements.
Check for Clashes: Review the wall section for any clashes or conflicts between different building systems, such as MEP clashes with structural elements or interference between finishes and structural components.
Seek Feedback and Revision: After completing the initial drawing, seek feedback from peers, supervisors, or professionals to identify any errors or areas for improvement. Revise the drawing as needed to ensure accuracy and completeness.